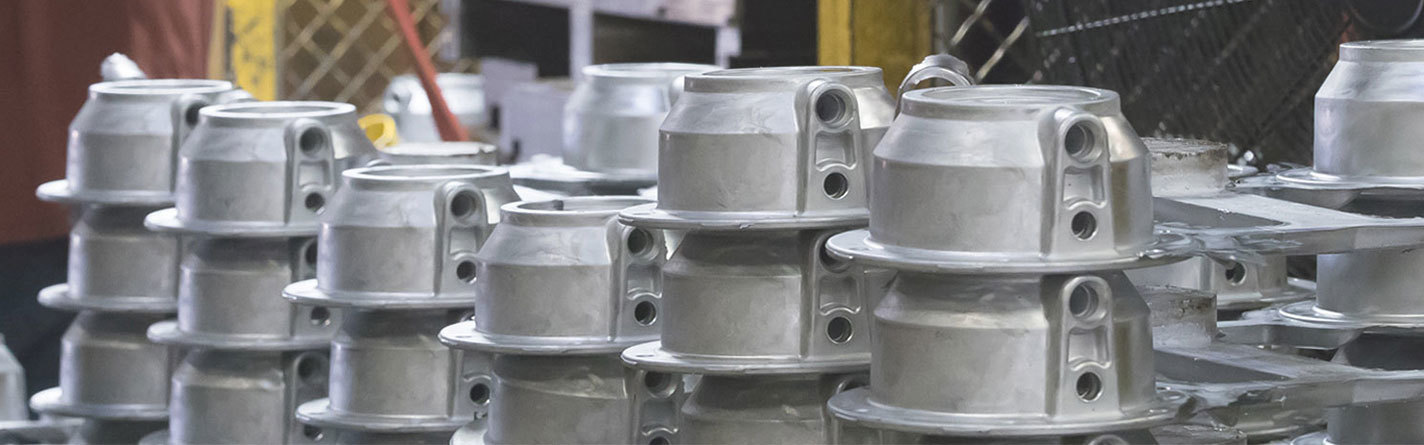
Customized products can be provided according to drawings
Low Pressure Die Casting
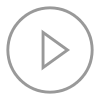
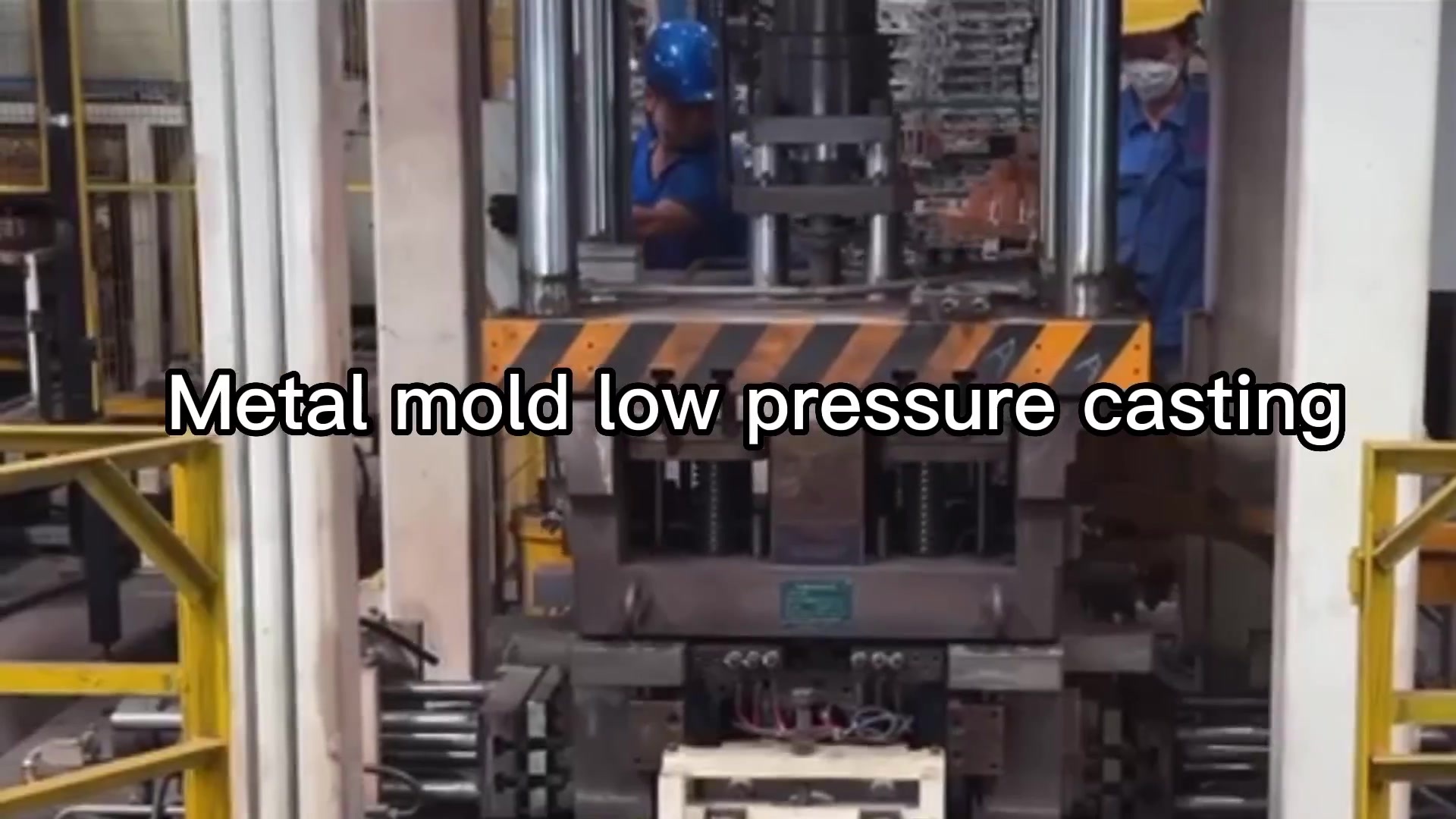
What is Low Pressure Die Casting?
- Low Pressure Die Casting Materials
Material Type | Typical Grade | Features |
Aluminum Alloys | A356 | Good mechanical properties Corrosion resistance Easy to process |
A380 | High strength Good fluidity Suitable for complex shapes | |
A360 | Higher tensile strength Good ductility | |
Magnesium Alloys | AZ91D | Excellent specific strength and stiffness Lightweight Good corrosion resistance |
AM60B | Higher ductility Good impact resistance | |
Zinc Alloys | ZAMAK 3 | Good fluidity and surface finish Cost-effective |
ZAMAK 5 | Higher strength and hardness Good corrosion resistance | |
Copper Alloys | Brass (C26000) | Good electrical and thermal conductivity Good machinability |
Bronze (C95500) | High strength and wear resistance Good corrosion resistance |
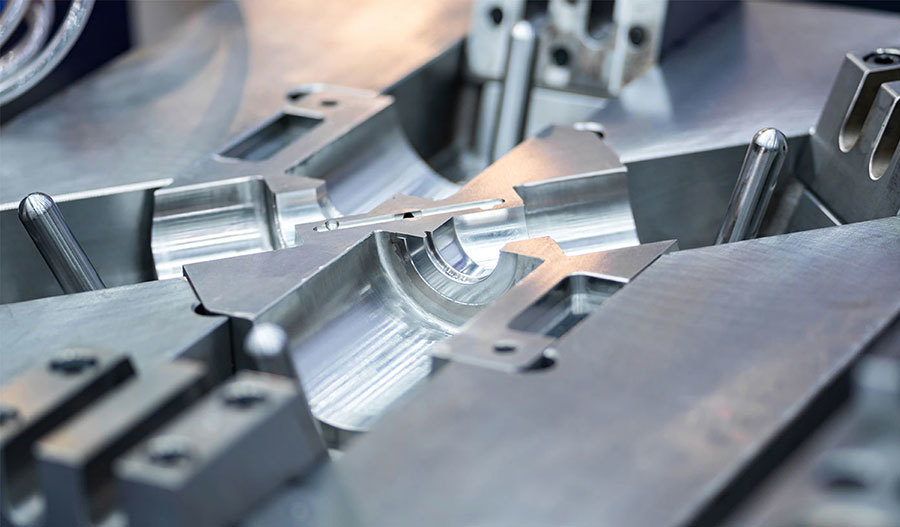
Low Pressure Die Casting Process
1. Prepare the Mold
● Clean and Inspect the Mold:
▶ Thoroughly clean the mold using compressed air or cleaning agents to remove any residues or contaminants.
▶ Check the mold for any damage or wear and repair it if necessary.
● Apply Release Agent:
▶ Apply a release agent evenly to the mold surface to prevent the casting from sticking and to facilitate ejection.
▶ Choose the right release agent to ensure it does not affect the surface quality or subsequent processing.
2. Melt the Metal
● Prepare Metal Raw Materials:
▶ Select the appropriate metal raw materials based on the required casting material, such as aluminum or magnesium alloys.
▶ Weigh the metal raw materials to ensure the correct amount for the casting.
● Melt the Metal:
▶ Place the metal raw materials in a furnace and heat them to above their melting point to ensure complete melting and a consistent temperature.
▶ Use induction heating or resistance heating to melt the metal, ensuring uniform and stable temperatures.
● Adjust Melting Temperature:
▶ Adjust the melting temperature according to the material requirements. For example, aluminum alloys typically melt around 660°C, while magnesium alloys melt around 650°C.
▶ Maintain a stable melting temperature to avoid fluctuations that could affect the metal's fluidity.
3. Preheat the Mold
● Preheat the Mold:
▶ Preheat the mold to a certain temperature to reduce thermal stress and prevent cold cracking.
▶ Typically, preheat the mold to between 200-300°C.
● Check Preheating Effect:
▶ Use an infrared thermometer or other temperature measurement tools to ensure the mold is uniformly heated.
4. Fill the Mold
● Prepare the Riser Tube:
▶ Pour the melted metal into a sealed riser tube located below the mold.
▶ Ensure the riser tube is clear and free of obstructions.
● Fill the Mold:
▶ Use low-pressure gas (typically 0.7 to 15 psi) to push the molten metal from the riser tube into the mold cavity.
▶ Control the pressure and speed to ensure the metal flows smoothly into the mold, reducing the formation of porosity and turbulence.
▶ Monitor the filling process to ensure the mold cavity is completely filled without any voids.
5. Solidify and Cool
● Maintain Pressure:
▶ Keep the low-pressure gas applied until the metal fully solidifies to ensure the casting's density and structural integrity.
▶ The solidification time depends on the thickness and complexity of the casting, usually ranging from a few seconds to a few minutes.
● Cool the Casting:
▶ Gradually reduce the pressure to allow the metal to cool in the mold.
▶ The cooling time varies based on the size and material of the casting, typically from a few minutes to several minutes.
6. Open the Mold and Eject the Casting
● Open the Mold:
▶ Once the casting is fully cooled, open the mold.
▶ Use hydraulic or mechanical devices to open the mold smoothly to avoid damaging the casting.
● Eject the Casting:
▶ Use an ejection mechanism to remove the casting from the mold.
▶ Inspect the ejection process to ensure the casting detaches from the mold without any issues.
● Initial Inspection:
▶ Perform an initial inspection of the ejected casting to ensure there are no obvious defects or damages.
7. Clean and Post-Process
● Remove Gates and Risers:
▶ Cut off gates, risers, and other excess parts using cutting tools or grinding equipment.
▶ Ensure the removal process does not damage the main body of the casting.
● Machine the Casting:
▶ Perform necessary machining to achieve the final dimensions and surface finish.
▶ Use CNC machines or conventional machines for precision machining to ensure dimensional accuracy and surface smoothness.
● Surface Treatment:
▶ Apply surface treatments such as painting, anodizing, or plating to improve corrosion resistance and aesthetics.
▶ Choose the appropriate surface treatment method to meet the required performance and appearance standards.
8. Quality Inspection
● Visual Inspection:
▶ Inspect the casting visually to ensure there are no cracks, porosity, or inclusions.
▶ Use magnifying glasses or microscopes to check fine details.
● Dimensional Inspection:
▶ Measure the casting's dimensions using calipers, micrometers, or other measuring tools to ensure they meet design specifications.
▶ Record measurement data for statistical analysis.
● Non-Destructive Testing:
▶ Perform non-destructive testing (such as X-ray or ultrasonic testing) to check for internal defects.
▶ Ensure the casting has a sound internal structure with no porosity or cracks.
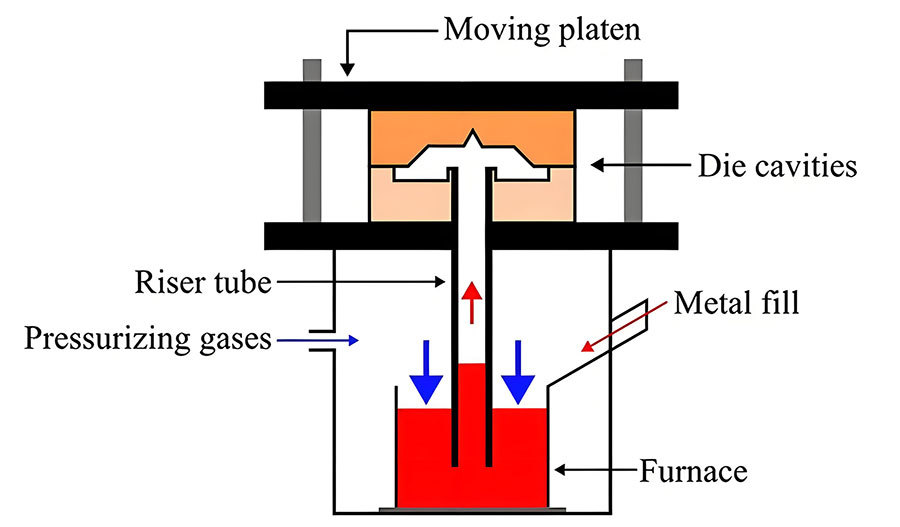
Low Pressure Die Casting Applications
Low-pressure die casting is an efficient casting technology that is particularly suitable for producing high-quality, dimensional-accurate and complex metal parts. This technology has a wide range of applications, especially in the automotive industry and other fields that require precision castings. The following are the main applications of low-pressure die casting:
Industry | Application Examples |
Automotive | Produces wheels, engine components, brake system parts, and suspension system parts. |
Aerospace | Manufactures structural and functional components for aircraft and spacecraft. |
Electronics | Creates enclosures and internal support structures for electronic devices. |
Machinery | Produces pump bodies, valve bodies, and other mechanical parts. |
Consumer Goods | Makes components for sports equipment and home appliances. |
Renewable Energy | Used in the production of battery boxes for electric vehicles. |
The Advantages & Disadvantages of Low Pressure Die Casting
- Advantages of Low Pressure Die Casting
1. Better Filling Control
● Smooth Filling: Low pressure die casting uses low pressure to inject molten metal smoothly into the mold, reducing the formation of porosity and turbulence, which improves the quality and density of the casting.
● Precise Control: By precisely controlling the filling speed and pressure, the process better manages metal flow, reducing defect formation.
2. Improved Mechanical Properties
● Uniform Microstructure: With slow filling under low pressure, the microstructure of the casting becomes more uniform, with finer grains, enhancing mechanical properties such as strength and toughness.
● Higher Density: Low pressure die casting produces higher-density castings, reducing internal defects and improving overall performance.
3. Reduced Defects
● Less Porosity: Low pressure die casting reduces the formation of porosity, increasing the density and strength of the casting.
● Fewer Cracks: Smooth filling processes reduce thermal stress and the risk of cold cracking, decreasing the likelihood of cracks forming.
4. High Surface Finish
● Quality Surface: Low pressure die casting produces castings with a high surface finish, reducing the need for secondary machining and lowering production costs.
● Reduced Surface Treatment: The high-quality surface reduces the need for additional surface treatments, saving time and resources.
5. High Production Efficiency
● High Automation: The process is highly automated, with short production cycles, making it suitable for mass production and increasing efficiency.
● Continuous Production: Continuous production is possible, reducing downtime and manual intervention, further boosting efficiency.
6. High Material Utilization
● Reduced Waste: The process maximizes the use of metal, reducing waste and lowering production costs.
● Recycling: Unused metal can be recycled, further conserving resources.
7. Wide Application Range
● Multiple Materials: Low pressure die casting works well with various materials, such as aluminum and magnesium alloys, and is widely used in automotive, aerospace, and electronics industries.
● Complex Shapes: It can produce parts with complex shapes, thin walls, and high precision, meeting diverse industry needs.
8. Environmentally Friendly
● Low Energy Consumption: Compared to high-pressure die casting, low pressure die casting consumes less energy, making it more environmentally friendly.
● Reduced Pollution: The process generates less waste, minimizing environmental impact.
- Disadvantages of Low Pressure Die Casting
1. High Equipment Investment
● Initial Cost: The initial investment for low pressure die casting equipment, including molds, furnaces, and control systems, is relatively high, which can be a burden for small and medium-sized enterprises.
● Maintenance Costs: Maintenance and upkeep of the equipment can also be costly, requiring regular inspections and replacement of wear parts.
2. High Mold Cost
● Complex Design: Designing and manufacturing molds for low pressure die casting is expensive, especially for parts with complex shapes, requiring high technical and cost inputs.
● Expensive Materials: Molds are typically made from high-quality materials to ensure durability and precision, adding to the cost.
3. Low Production Flexibility
● Difficult Design Changes: Once a mold is designed, changing the product design is challenging and requires designing and manufacturing new molds, increasing time and costs.
● Poor Adaptability: The process is less adaptable to quick product changes, requiring longer preparation times.
4. Size Limitations
● Medium-Sized Castings: Low pressure die casting is best suited for medium-sized castings. Very large or very small castings may be better produced using other casting methods.
● Weight Restrictions: For heavier castings, the filling and cooling capabilities of low pressure die casting may be insufficient.
5. Long Initial Setup Time
● Complex Debugging: Debugging and optimizing new molds can take a long time, involving multiple trials and adjustments to ensure high-quality castings.
● Parameter Adjustment: Precisely adjusting parameters such as pressure, temperature, and filling speed requires skilled operators and technical support.
6. Complex Process
● Multiple Parameters: The process involves controlling multiple parameters, such as pressure, temperature, and filling speed, which requires experienced operators and technical expertise.
● High Technical Requirements: Operators need high levels of technical skill and experience, and training qualified personnel takes time and resources.
We would be happy to connect with you.
We will contact you within one working day. Please pay attention to your email.