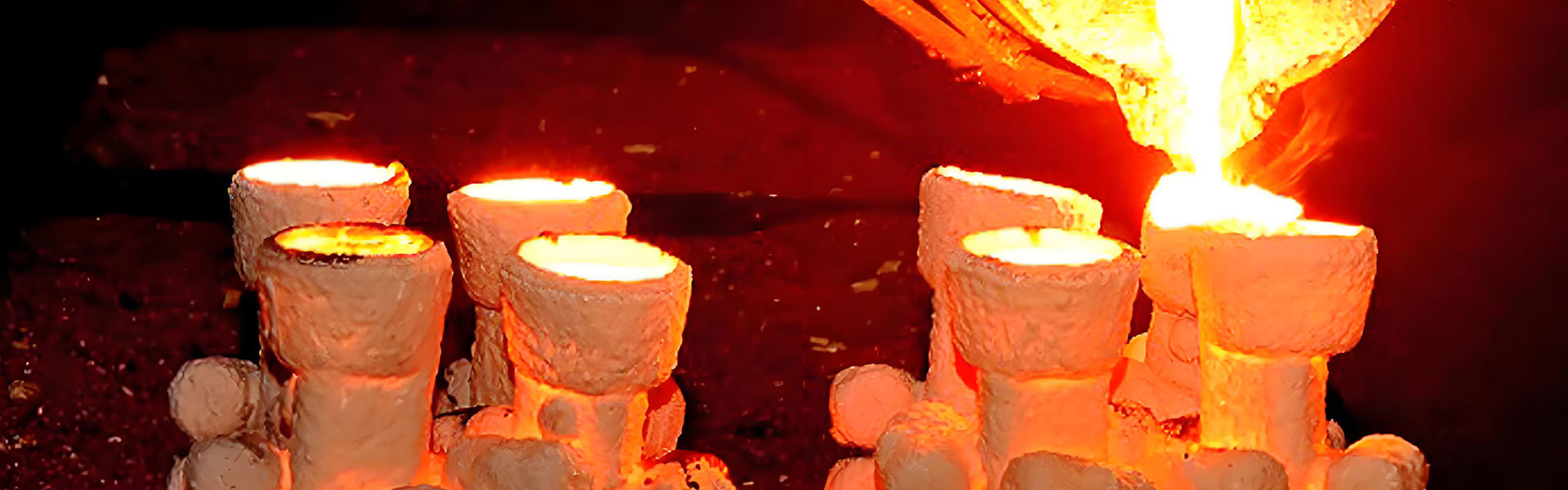
Customized products can be provided according to drawings
Lost Wax Investment Casting
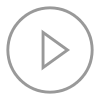
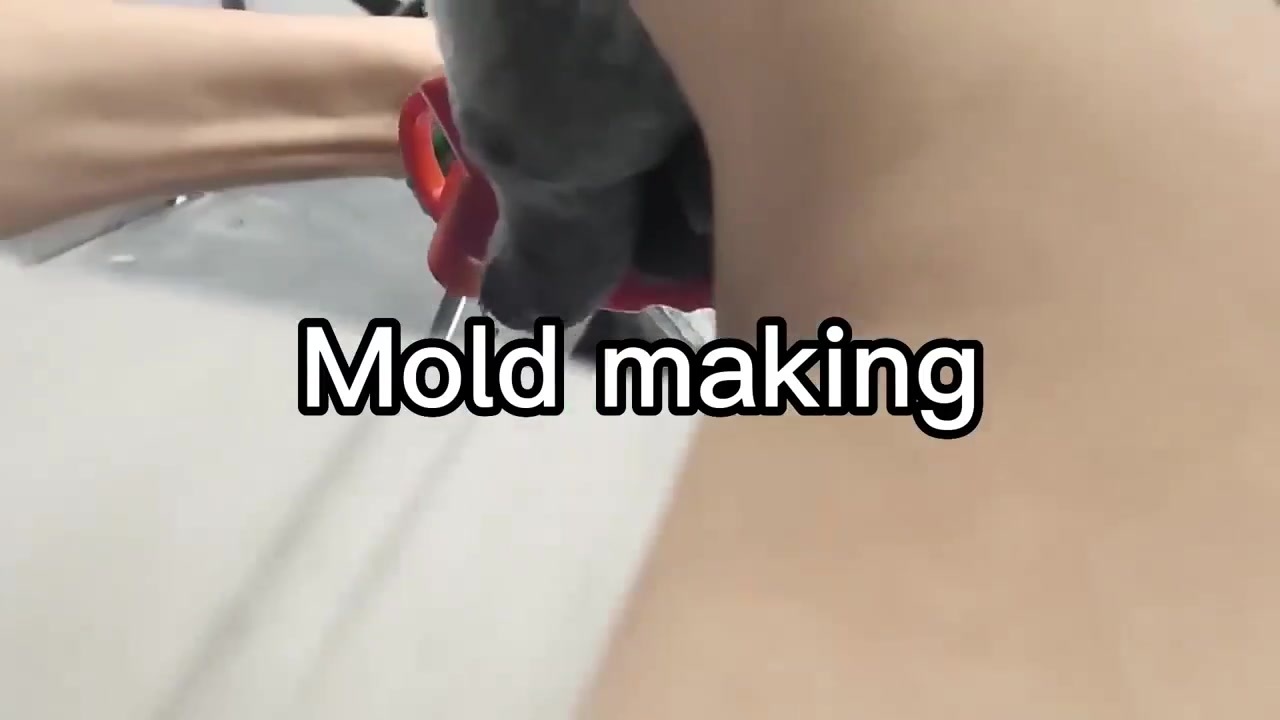
What is Investment Casting?
- Investment Casting Materials
Investment casting is a highly precise casting technology that produces high-precision and complex-shaped metal castings by using fusible wax patterns to make casting molds. Its main advantages include excellent accuracy and surface finish, with dimensional accuracy of ±0.05% to ±0.1% and surface finish of Ra 1.6 μm, reducing the need for subsequent processing. It is suitable for a variety of metal materials, such as carbon steel, alloy steel, stainless steel, copper alloy, aluminum alloy, titanium alloy and precious metals.
Material Type | Metal Grades | Properties |
Carbon Steel | AISI 1020, AISI 1045, AISI 1080 | Varies with carbon content; good strength and hardness |
Alloy Steel | AISI 4140, AISI 4340, AISI 8620 | High strength, hardness, wear resistance, and corrosion resistance |
Stainless Steel | 304, 316, 17-4 PH, 17-7 PH | Excellent corrosion and oxidation resistance |
Copper Alloys | C11000 (Electrolytic Copper), C36000 (Brass), C95500 (Aluminum Bronze) | Good electrical and thermal conductivity, good mechanical properties |
Aluminum Alloys | 2024, 6061, 7075 | Lightweight, high strength-to-weight ratio, good corrosion resistance |
Titanium Alloys | Ti-6Al-4V, Ti-5Al-2.5Sn | High specific strength, excellent corrosion resistance, biocompatibility |
The Investment Casting Process
1. Pattern Making
● Design and Prototyping: Start by creating a precise prototype based on the product design or 3D model. This step is crucial for ensuring the final product meets quality and functional requirements.
● Wax Pattern Production: Use the prototype as a template to produce multiple wax patterns through injection molding. The wax material typically used is specialized casting wax, which has good flowability and easy demolding properties.
2. Assembly
● Pattern Tree Construction: Assemble multiple wax patterns into a "tree" structure, also known as the gating system. Arrange the patterns in a way that ensures they will be correctly positioned during the casting process.
● Securing Patterns: Use specialized tools to securely attach the wax patterns to the main trunk of the gating system, ensuring they remain in place during pouring.
3. Shell Building
● Initial Dip: Dip the assembled wax pattern tree into a refractory slurry to completely coat it. This forms the first layer of the ceramic shell.
● Coating with Sand: Immediately after dipping, immerse the coated tree in fine sand or spray it with a sandblaster to ensure a uniform layer of refractory material covers the surface.
● Drying: Place the coated tree in a well-ventilated area to dry naturally, or use hot air to speed up the drying process. Ensure each layer dries thoroughly before applying the next.
● Building Multiple Layers: Repeat the dipping and coating process multiple times to build up the thickness and strength of the ceramic shell until it meets the required specifications.
4. Dewaxing
● Heating: Place the completed ceramic shell in a heating furnace and gradually increase the temperature to melt the wax inside.
● Collecting Wax: Collect the melted wax for recycling and reuse.
5. Firing
● High-Temperature Treatment: Continue to raise the temperature to perform high-temperature firing, which removes any remaining organic materials and hardens the ceramic shell.
● Cooling: Allow the ceramic shell to cool slowly to prevent thermal shock and cracking.
6. Pouring
● Metal Preparation: Select the appropriate metal material, such as stainless steel or nickel-based alloys, and melt it into a liquid state.
● Pouring Metal: Pour the molten metal into the ceramic shell through the gating system, ensuring it fully fills the cavity.
● Cooling: Let the metal solidify and cool naturally within the shell, or apply forced cooling if necessary.
7. Shell Removal and Cleaning
● Breaking the Ceramic Shell: Use hammers, vibratory equipment, or chemical solvents to carefully remove the outer ceramic shell.
● Finishing: Grind and clean the cast part to remove any remnants of the gating system and other excess material, ensuring a smooth and clean surface.
8. Inspection and Finishing
● Quality Inspection: Perform dimensional, visual, and performance inspections on the cast part to ensure it meets the design requirements.
● Post-Processing: Depending on the needs, conduct additional machining, surface treatments, or other finishing processes to achieve the final product specifications.
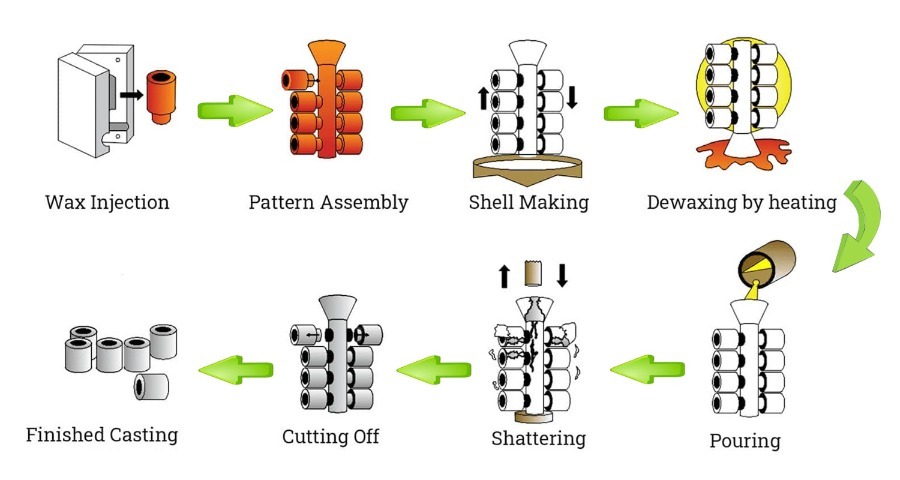
Investment Casting Applications
Application Area | Specific Examples |
Aerospace | Engine components (turbine blades, nozzles, combustion chambers) Structural parts (landing gear, connectors, brackets) Precision instruments (navigation systems, sensors) |
Automotive | Engine parts (turbochargers, valves, pistons) Exhaust systems (exhaust pipes, mufflers) Transmission systems (gears, shafts) |
Medical Devices | Surgical instruments (scissors, clamps, needles) Implants (artificial joints, dental implants) Diagnostic equipment (CT scanners, MRI machines) |
Jewelry Manufacturing | Custom jewelry (rings, necklaces, bracelets) Artistic decorations (sculptures, trophies) |
Industrial Equipment | Pumps and valves (pump impellers, valve bodies, valve cores) Turbines (steam turbines, gas turbine blades and discs) Molds and tools (stamping dies, cutting tools) |
Electronics | Connectors (connectors and terminals in various electronic devices) Enclosures (casings and frames for precision electronic devices) |
Energy Industry | Power generation equipment (generator rotors, stators) Oil and gas (drilling equipment, pipeline connectors) |
Sports Equipment | Golf equipment (golf club heads, grips) Bicycle components (frames, cranks) |
Household Items | Kitchen utensils (knives, cutlery) Home decor (light fixtures, decorative items) |
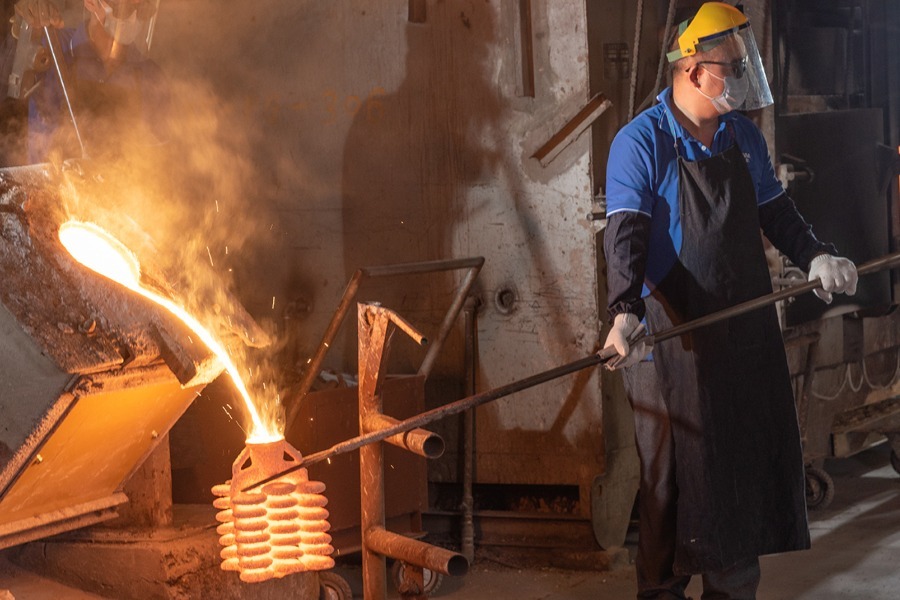
The Advantages & Disadvantages of Investment Casting
- Advantages of Investment Casting
1. High Precision
● Complex Shapes: Investment casting can produce highly complex shapes and intricate details, making it ideal for parts with complex geometries.
● Dimensional Accuracy: The use of wax patterns and ceramic shells ensures high dimensional accuracy, typically achieving IT7-IT8 tolerance levels.
2. Excellent Surface Finish
● Reduced Post-Processing: The smooth surface finish often eliminates or minimizes the need for additional machining, reducing production costs and time.
● Aesthetic Quality: For items requiring a visually appealing surface, such as jewelry and decorative pieces, investment casting provides superior surface quality.
3. Material Versatility
● Wide Range of Metals: This process works with a variety of metals and alloys, including stainless steel, nickel-based alloys, titanium, and aluminum, catering to diverse industry needs.
● High-Performance Materials: It can produce parts from high-strength, heat-resistant, and corrosion-resistant materials.
4. Cost-Effective for Small Batches
● Economical for Limited Runs: Investment casting offers cost-effective solutions for small batch productions of high-precision parts.
● Low Scrap Rate: The high precision and reliability of the process result in a low scrap rate, reducing material waste.
5. Design Flexibility
● Customization: Designs can be tailored to meet specific customer requirements, allowing for the production of personalized and specialized parts.
● Rapid Prototyping: Quick prototyping techniques enable rapid design validation, accelerating the product development cycle.
- Disadvantages of Investment Casting
1. Higher Costs
● Initial Investment: High initial costs for equipment and mold production make investment casting less suitable for large-scale production.
● Longer Production Cycle: The entire process from pattern making to final casting takes longer, making it less suitable for urgent orders.
2. Complex Process
● Multiple Steps: The process involves several steps, including pattern making, assembly, shell building, dewaxing, firing, and pouring, each requiring strict control.
● Technical Expertise: Operators need high levels of skill and experience to ensure quality at each stage.
3. Material Limitations
● High-Melting-Point Metals: While applicable to many metals, casting high-melting-point metals like tungsten and molybdenum is more challenging and costly.
● Special Alloys: Some special alloys may develop porosity or inclusions during melting, affecting the quality of the cast parts.
4. Environmental Impact
● Resource Consumption: The process uses significant amounts of refractory materials and energy, impacting the environment.
● Waste Management: Proper disposal of ceramic shells and wax patterns is necessary to avoid environmental pollution.
5. Size Limitations
● Large Parts: Investment casting is more suitable for small to medium-sized parts, with limitations for larger components.
● Weight Constraints: Parts produced typically weigh less than a few dozen kilograms due to process constraints.
6. Surface Defects
● Porosity and Inclusions: Despite the smooth surface finish, cast parts may occasionally exhibit porosity or inclusions, affecting performance.
● Dimensional Changes: High temperatures during processing can cause slight dimensional changes, requiring post-casting adjustments.
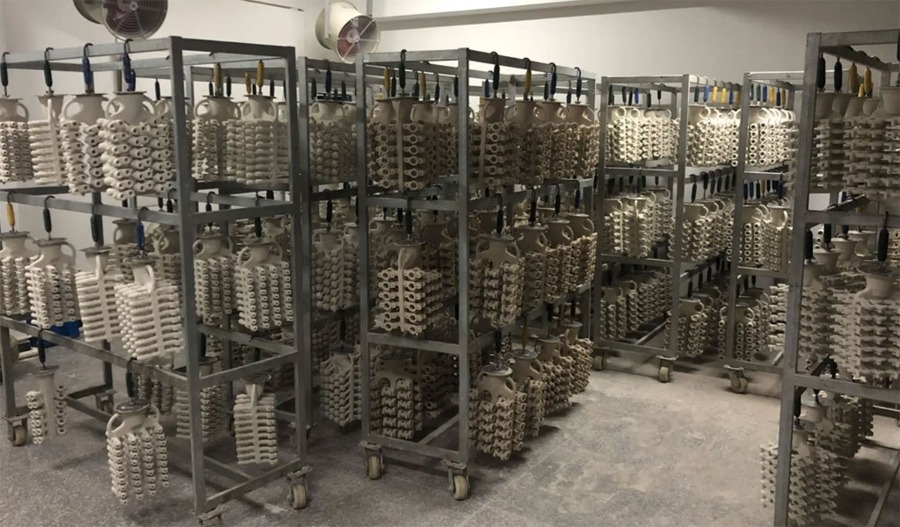
We would be happy to connect with you.
We will contact you within one working day. Please pay attention to your email.