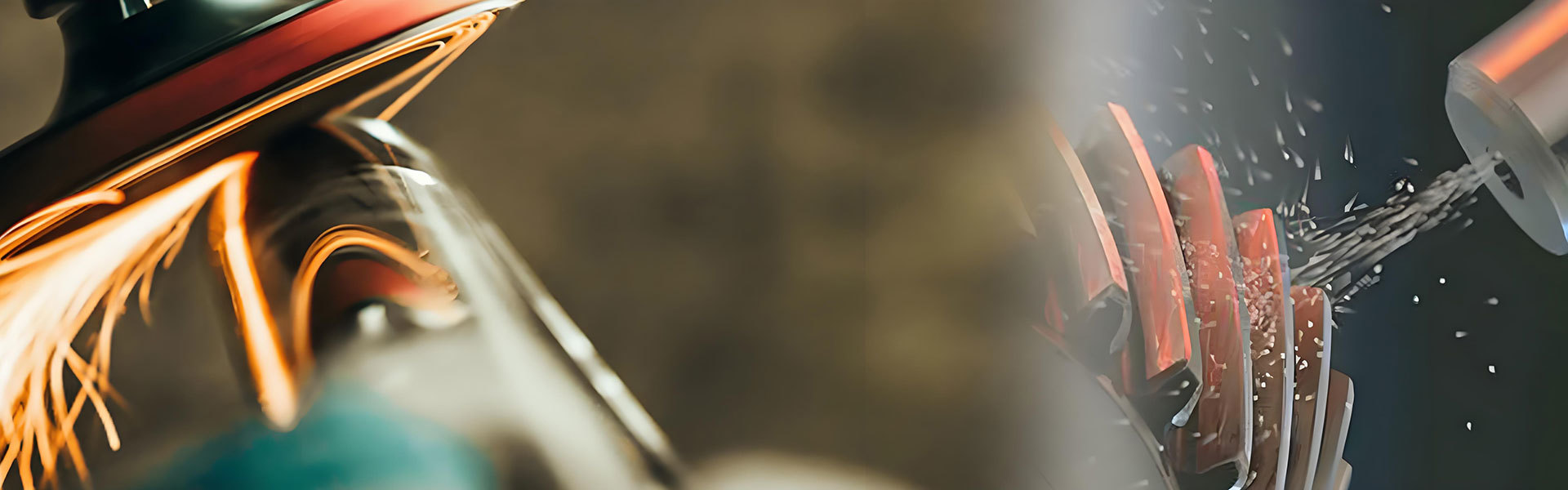
Customized products can be provided according to drawings
Surface Treatment
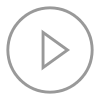
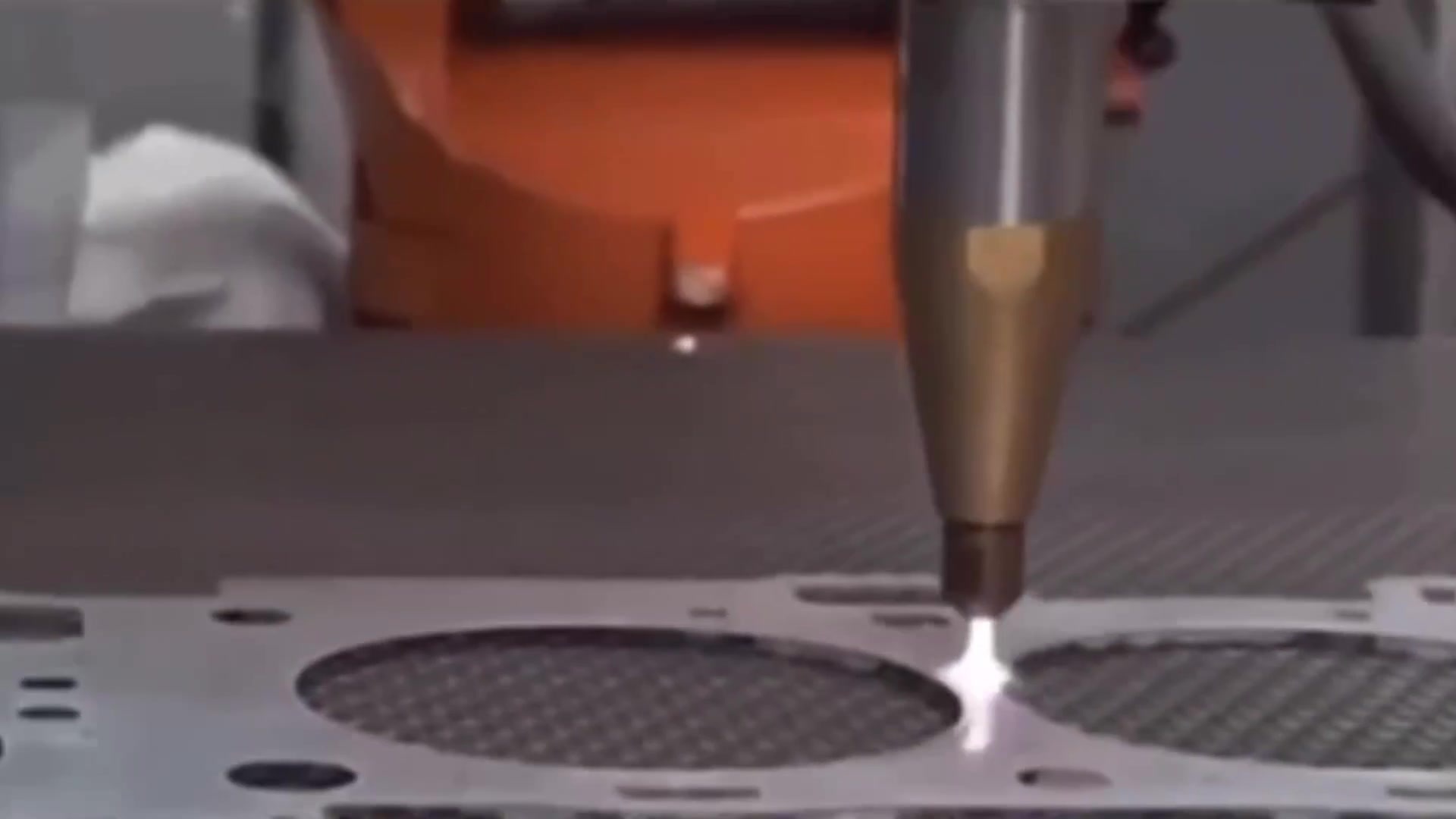
What is Surface Treatment?
Surface treatment involves specific processes applied to the surface of an object to achieve desired effects. These effects may include increased corrosion resistance, improved wear resistance, enhanced electrical conductivity or insulation, and better aesthetics. By using various surface treatment methods, industries can meet their specific requirements for product characteristics.
For instance, in the automotive industry, body painting serves not just for aesthetics but also to prevent metal components from rusting, thereby extending the car's lifespan. In the electronics sector, circuit board plating ensures good electrical connections while providing necessary protection.
Moreover, surface treatment addresses environmental concerns. As societal awareness of environmental protection grows, more surface treatment techniques focus on reducing pollution and conserving resources. For example, using water-based coatings instead of solvent-based ones reduces harmful emissions and aligns with sustainable development goals.
In summary, surface treatment is more than just altering the surface of materials; it is a complex technology involving physics, chemistry, and other disciplines. It plays an indispensable role in improving product quality, promoting industrial upgrading, and achieving green production. Through continuous innovation and the development of new surface treatment technologies, we can better address future challenges and create a better living environment.
- Surface Treatment Processes: Features and Suitable Materials
Surface Treatment Technology |
Features |
Applicable Materials |
Electroplating |
Enhances corrosion resistance wear resistanceand decorative appearance improves conductivity |
Steel, stainless steel, copper, brass, bronze, aluminum, magnesium, zinc, nickel, silver, gold |
Polishing |
Increases surface gloss and smoothness, enhances aesthetics |
Steel, stainless steel, copper, aluminum, zinc, silver, gold |
Powder Coating |
Excellent weather resistance, durable, wide range of colors |
Steel, stainless steel, aluminum, aluminum alloys, galvanized steel, iron, copper, magnesium alloys |
Sandblasting |
Cleans surface contaminants, increases roughness, improves coating adhesion |
Steel, stainless steel, cast iron, aluminum, copper, zinc, titanium |
Metal Brushing |
Creates linear texture, enhances product feel |
Stainless steel, aluminum, aluminum alloys, copper, brass, bronze, titanium |
Anodizing |
Enhances corrosion resistance, can be colored, increases surface hardness |
Aluminum, aluminum alloys (such as 6061, 7075, 2024 aerospace-grade aluminum), magnesium alloys, titanium alloys |
Electrophoresis |
Uniform coating, suitable for complex-shaped parts, excellent corrosion resistance |
Steel, stainless steel, aluminum, aluminum alloys, copper, magnesium alloys, zinc alloys |
Shot Blasting |
Strengthens the surface, relieves residual stress, improves fatigue strength |
Steel, stainless steel, cast iron, aluminum, aluminum alloys, copper, titanium alloys, commonly used in springs, gears, crankshafts, connecting rods, etc. |
Phosphating |
Forms a phosphate protective film, improves rust resistance and paint adhesion |
Steel, cast iron, zinc alloys, aluminum alloys, widely used in automotive, home appliances, building hardware, etc. |
Baking Paint |
Vivid colors, excellent weather resistance, easy to clean |
Steel, stainless steel, aluminum, aluminum alloys, galvanized steel, iron, copper |
Electroplating
Electroplating is a process that uses electrolysis to deposit metal onto the surface of a substrate. By applying an electric current in an electrolyte, metal ions are reduced and deposited on the cathode (the object to be plated) to form a metal coating. The main principles include electrolyte, power supply, anode and cathode. The characteristics of electroplating include enhanced corrosion resistance, improved wear resistance, improved conductivity, increased decorativeness and repaired dimensions. It has a wide range of applications, such as the automotive industry, electronics industry, aerospace, decorations and hardware tools. The process includes pre-treatment (cleaning and activating the substrate surface), electroplating (putting the substrate into the electrolyte and applying electricity) and post-treatment (cleaning, drying, and inspecting the quality of the coating).
Polishing
Polishing refers to a processing method that uses mechanical, chemical or electrochemical effects to reduce the surface roughness of a workpiece to obtain a bright and smooth surface. Polishing cannot improve the dimensional accuracy or geometric shape accuracy of a workpiece, but is intended to obtain a smooth surface or mirror gloss, and is sometimes used to eliminate gloss. Polishing technology is widely used in the surface treatment of various materials such as metals, plastics, glass, and stone to improve the aesthetics and physical properties of the materials, such as increasing wear resistance, reducing friction, and improving corrosion resistance.
Powder Coating
Powder coating is a surface treatment technology widely used in surface coating of metal products. It uses fine solid powder particles as coating, and the powder is attached to the workpiece to be coated by electrostatic spraying or fluidized bed, and then heated and cured to form a solid, uniform and smooth protective film or decorative layer. The formed coating has high hardness, corrosion resistance, wear resistance, long-lasting color, and is not prone to defects such as sagging and dripping. It is suitable for various metal materials, such as steel, aluminum and its alloys, and can also be used for some non-metallic materials.
Sandblasting
Sandblasting is a process for surface treatment of workpieces. Compressed air is used as the power to form a high-speed jet beam to spray the material (copper ore sand, quartz sand, corundum, iron sand, sea sand) at high speed onto the surface of the workpiece to be treated, so as to achieve the purpose of cleaning, rust removal, deburring, and increasing roughness. Sandblasting is widely used in many fields such as metal processing, automobile maintenance, architectural decoration, and art restoration.
Metal Brushing
Metal brushing is a surface treatment process that forms a thin line-like texture on the metal surface through mechanical action, thus giving the metal surface a special visual effect and touch. This process can not only improve the aesthetics of the product, but also has certain practical functions, such as increasing friction and reducing fingerprint marks. Metal brushing is widely used in the surface treatment of metal materials such as stainless steel products, aluminum products, and copper products. Metal brushing is to use abrasive tools with specific textures (such as grinding wheels, sanding belts, wire brushes, etc.) to rub the metal surface at high speed to form fine linear scratches on the metal surface. These scratches are arranged in an orderly manner to form a unique texture effect.
Anodizing
Anodizing is a surface treatment process. The basic principle is to use metal as an anode in an electrolyte to generate a dense oxide film on the metal surface through the action of direct current. It is mainly used in metal materials such as aluminum alloys to form a dense oxide film on the metal surface through the electrolysis process. This oxide film not only improves the corrosion resistance and wear resistance of the metal, but also can give the metal surface rich colors through dyeing. Anodizing is widely used in aerospace, automotive, construction, electronics, consumer products and other fields.
Electrophoresis
Electrophoresis is a surface treatment process. The basic principle is to use the electric field to make the charged paint particles migrate in an electrolyte in a directional manner and deposit on the metal surface to form a uniform coating. It is mainly used to deposit an organic coating on the metal surface to improve its corrosion resistance, wear resistance and appearance quality. Electrophoretic coating technology is widely used in automobiles, home appliances, construction, electronics and other industries.
Shot Blasting
Shot blasting is one of the effective methods to reduce part fatigue and increase service life. Shot blasting is to spray a high-speed shot stream onto the surface of the part, causing plastic deformation on the surface of the part to form a reinforced layer of a certain thickness. Due to the existence of compressive stress on the surface of the part, part of the stress can be offset when the part is subjected to load, thereby improving the fatigue strength of the part. Shot blasting is widely used in aviation, automobiles, ships, machinery manufacturing and other industries, and can significantly improve the surface quality and service life of metal parts.
Phosphating
Phosphating is an important surface treatment process that forms a phosphate conversion film on the metal surface through chemical reaction to improve the metal's corrosion resistance, wear resistance and coating adhesion. The basic principle is to immerse the metal workpiece in a solution containing phosphate and generate a uniform phosphate conversion film on the metal surface through chemical reaction. This film can not only improve the corrosion resistance of the metal, but also improve the adhesion of the coating, preparing for subsequent painting, electroplating and other processes. Phosphating is widely used in industries such as automobiles, home appliances, construction, and machinery manufacturing.
Baking Paint
Baking paint is a surface treatment process. The basic principle is to spray liquid or powder coating on the surface of the substrate, and then bake it at high temperature to solidify the coating to form a strong protective layer. The baking process is widely used in automobiles, home appliances, furniture, construction and other industries, and can significantly improve the aesthetics and durability of products.
We would be happy to connect with you.
We will contact you within one working day. Please pay attention to your email.