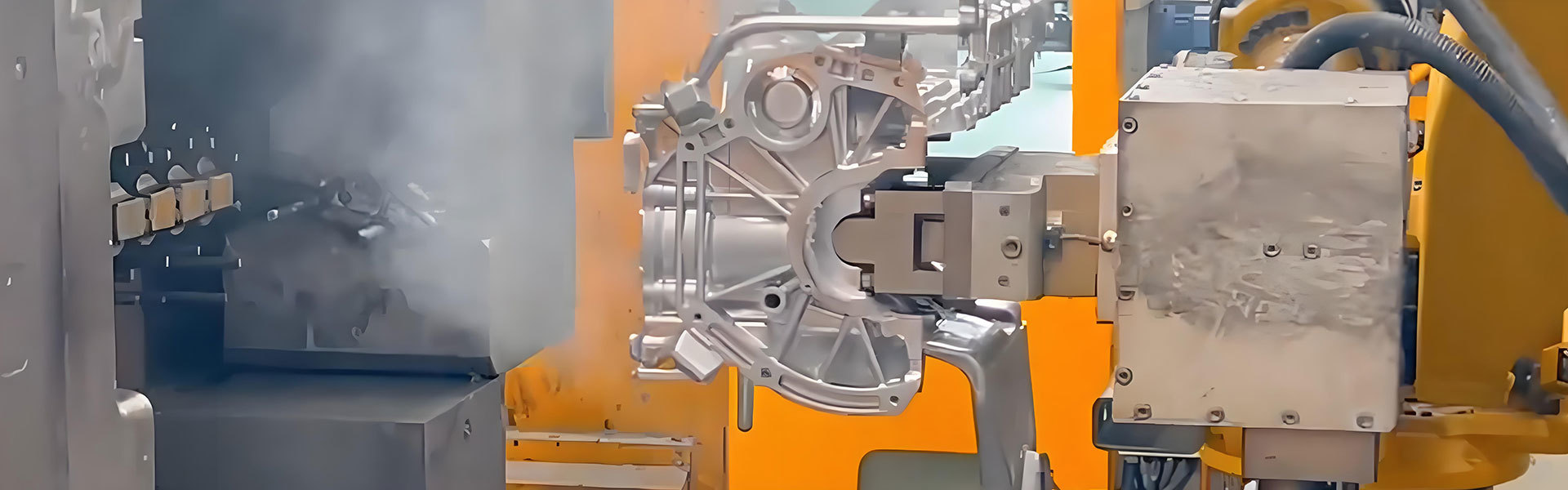
Customized products can be provided according to drawings
High Pressure Die Casting
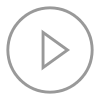
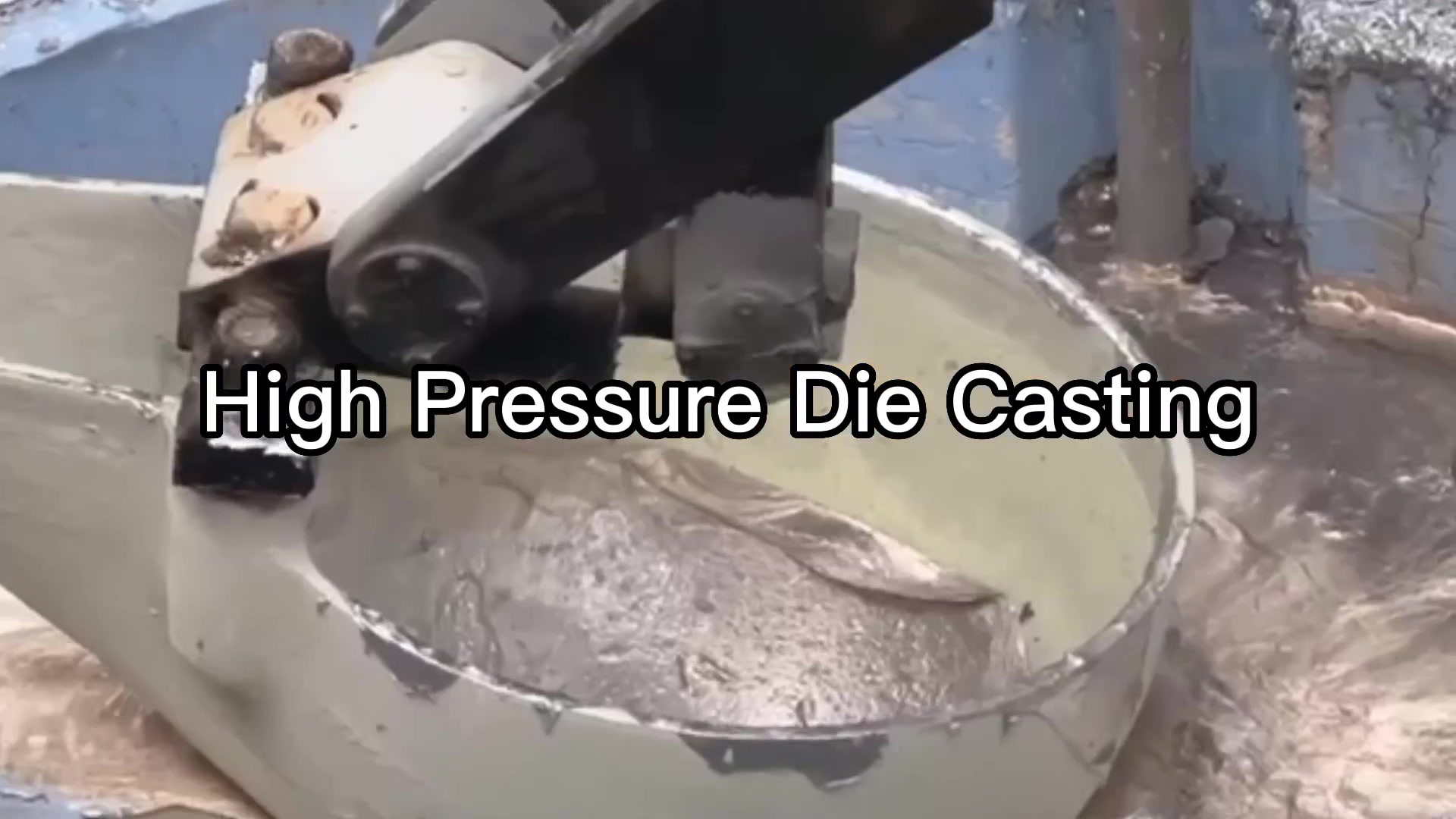
What is High-Pressure Die Casting?
- High Pressure Die Casting Materials
Material | Properties | Applications |
Aluminum Alloys | - Lightweight:Low density, ideal for light components - Corrosion Resistance:Good resistance to corrosion - Thermal Conductivity:Excellent for heat dissipation - Mechanical Properties:Moderate strength and hardness, suitable for various surface treatments | - Automotive:Engine blocks, transmission cases, wheels - Consumer Electronics:Smartphone and laptop casings - Household Appliances:Air conditioners, refrigerators |
Zinc Alloys | - Castability: Excellent flow, suitable for complex and detailed parts - Cost-Effective: Relatively inexpensive, ideal for high-volume production - Strength:High strength at room temperature - Surface Treatment: Easy to plate and paint | - Automotive:Decorative parts, small components - Consumer Electronics: Connectors, casings - Household Appliances:Switches, decorative parts |
Magnesium Alloys | - Extremely Light:Lowest density among practical metals - Strength and Stiffness:High strength and stiffness, suitable for structural components - Vibration Damping: Good vibration absorption - Processability:Easy to cast and machine | - Automotive: Instrument panels, seat frames - Aerospace:Internal aircraft structures - Consumer Electronics: Laptop casings, smartphone casings |
Copper Alloys | - High Strength:Excellent mechanical strength and wear resistance - Electrical and Thermal Conductivity:Superior for electrical and thermal applications - Corrosion Resistance:Good resistance to corrosion in various environments - Cost:Higher cost, suitable for high-performance applications | - Automotive:Radiators, connectors - Electronics:Circuit boards, terminals - Household Appliances:Heating elements, connectors |
High Pressure Die Casting Process
The basic principle of high-pressure die casting is to fill the die casting cavity with liquid or semi-liquid metal at a high speed under high pressure, and then form and solidify under pressure. The process includes the following steps:
1. Preparation:
● Preheat the die to a specific temperature.
● Apply a release agent to the die surface to ensure easy part ejection.
2. Clamping:
● Use a powerful hydraulic system to securely close the two halves of the die.
3. Injection:
● Inject molten metal into the die cavity at high speed and pressure through a system of runners and gates.
4. Cooling:
● The molten metal quickly cools and solidifies in the die due to the temperature difference between the hot metal and the cooler die surface.
5. Ejection:
● Once the metal has solidified, open the die, and use ejector pins to push the part out.
6. Trimming and Finishing:
● Remove excess material, such as flash or gates.
● Perform additional finishing processes if needed, such as machining or surface treatment.
Considerations
● Temperature Control: Ensure the die and molten metal are at the appropriate temperatures for optimal filling and cooling.
● Pressure Control: Maintain consistent high pressure to ensure the molten metal fully fills the die cavity.
● Cooling Time: Adjust the cooling time based on the size and thickness of the part to ensure proper solidification.
● Ejection Force: Use the appropriate ejection force to avoid damaging the part or the die.
By following these steps, high pressure die casting efficiently produces high-precision parts with complex geometries, suitable for a variety of industrial applications.
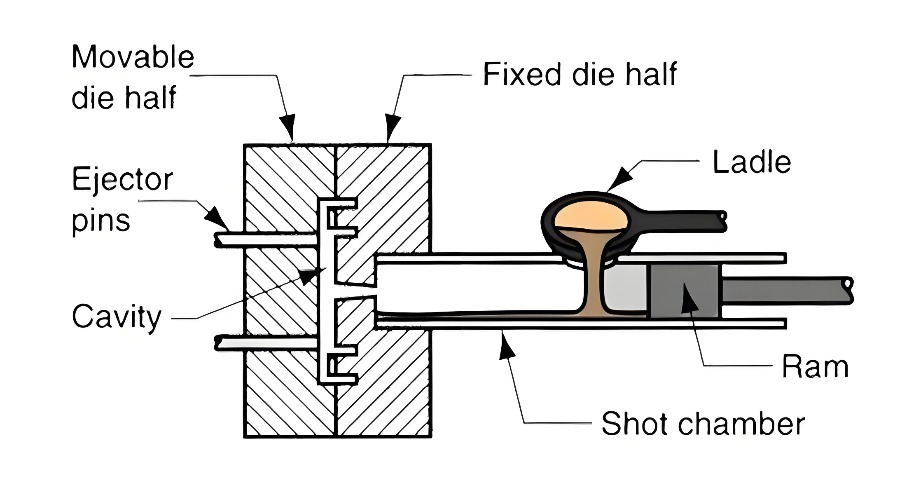
The minimum cross-sectional area and minimum draft angle corresponding to various materials are listed in the following table
Material | Minimum Cross-Sectional Area (mm²) | Minimum Draft Angle (°) |
Aluminum Alloys | 0.5 - 1.0 | 0.5 - 1.0 |
Zinc Alloys | 0.3 - 0.5 | 0.5 - 1.0 |
Magnesium Alloys | 0.5 - 1.0 | 0.5 - 1.0 |
Copper Alloys | 0.5 - 1.0 | 0.5 - 1.0 |
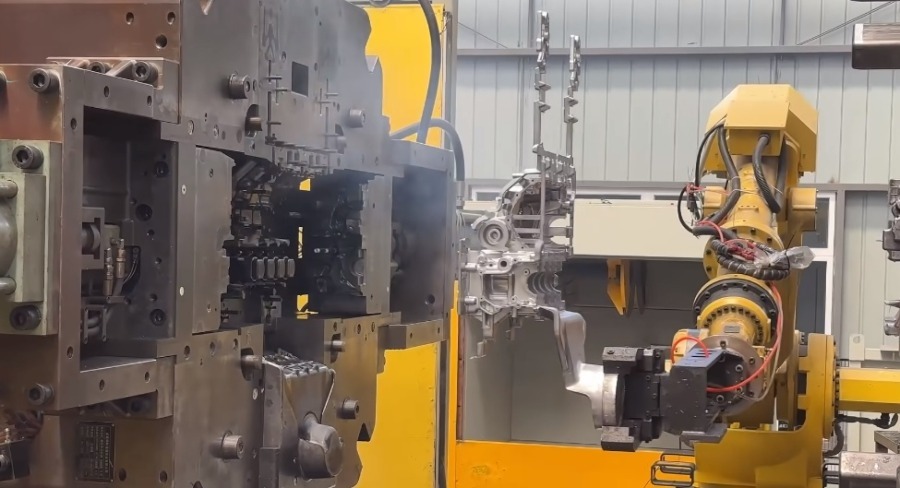
The Advantages & Disadvantages of High Pressure Die Casting
- Advantages of High Pressure Die Casting
1. High Production Efficiency: High-pressure die casting enables rapid production cycles, often completing a cycle in just a few seconds. This efficiency makes it perfect for mass production.
2. Complex Geometries: The process can create parts with intricate shapes and thin walls, which other casting methods might struggle to achieve.
3. Consistent Quality: Parts produced through high-pressure die casting boast excellent dimensional accuracy and surface finish, reducing the need for secondary machining.
4. Material Utilization: The process uses only the necessary amount of metal to fill the die cavity, minimizing waste.
5. Versatility: A wide range of materials, including aluminum, zinc, and magnesium alloys, can be used, catering to various application requirements.
- Disadvantages of High Pressure Die Casting
1. High Initial Costs: The initial investment in die casting equipment and tooling is significant. Precision-machined dies can be expensive.
2. Limited Size Range: High-pressure die casting is generally better suited for smaller to medium-sized parts. Larger parts may require other casting methods due to equipment limitations.
3. Material Constraints: Some metals, especially those with higher melting points like steel, are not practical for high-pressure die casting due to the extreme temperatures and pressures involved.
4. Porosity Issues: Rapid solidification can sometimes cause porosity in the castings, affecting the strength and durability of the parts. Post-casting treatments may be necessary to address these issues.
5. Design Flexibility: Once a die is created, modifying the design can be costly and time-consuming. This rigidity can be a drawback for projects requiring frequent design changes.
Overall, high-pressure die casting is a powerful technique for producing high-quality, complex parts efficiently, but it requires careful consideration of the associated costs and material constraints.
We would be happy to connect with you.
We will contact you within one working day. Please pay attention to your email.