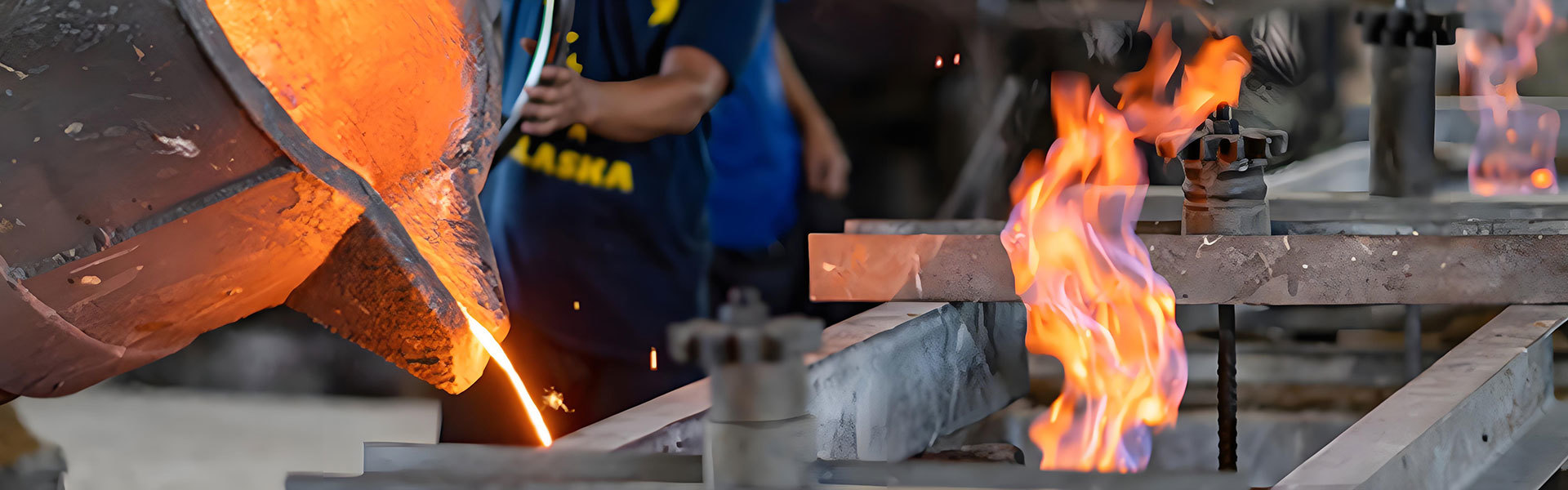
Customized products can be provided according to drawings
Sand Casting
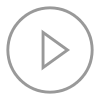
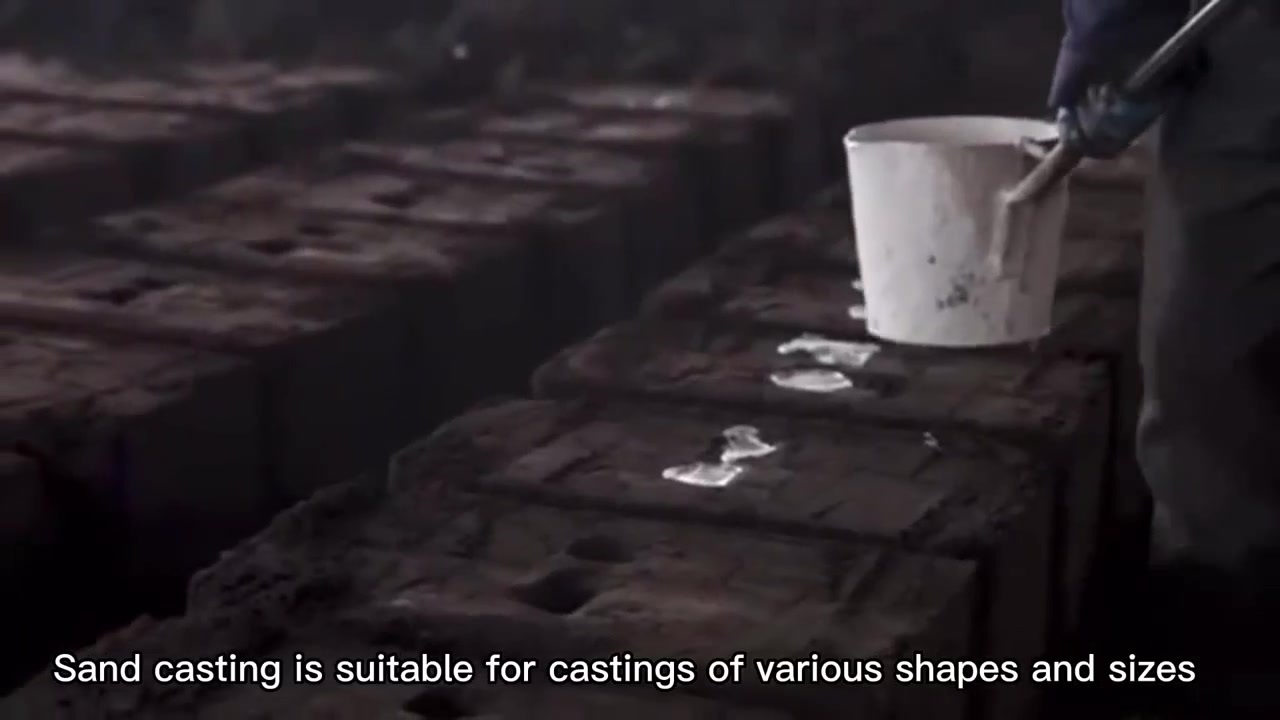
What is Sand Casting?
- Sand Casting Materials
Sand casting is a widely used metal forming technology that can use a variety of metals and alloys. The following are several materials commonly used in sand casting:
Material Category | Specific Materials |
Cast Iron | Gray Cast Iron |
Ductile Cast Iron (Nodular Iron) | |
Malleable Cast Iron | |
Cast Steel | Carbon Cast Steel |
Alloy Cast Steel | |
Aluminum Alloys | Aluminum-Silicon Alloys (Al-Si) |
Aluminum-Copper Alloys (Al-Cu) | |
Aluminum-Magnesium Alloys (Al-Mg) | |
Copper Alloys | Brass (Cu-Zn) |
Bronze (Cu-Sn) | |
Phosphor Bronze (Cu-Sn-P) | |
Magnesium Alloys | Magnesium-Aluminum Alloys (Mg-Al) |
Zinc Alloys | Zinc-Aluminum Alloys (Zn-Al) |
Titanium Alloys | Titanium-Aluminum Alloys (Ti-Al) |
These materials are widely used in sand casting due to their various properties and application requirements.
The Sand Casting Process
Sand casting is a widely used metal casting process that involves using sand as the primary material to create molds. Here is a detailed step-by-step explanation of how sand casting works:
● Step 1: Pattern Making
Design the Pattern: Create a pattern that is an exact replica of the final part, including any necessary allowances for shrinkage and machining. Patterns are typically made from wood, plastic, or metal.
Prepare the Pattern: Ensure the pattern is smooth and free of defects. It should be designed to be easily removed from the sand without damaging the mold.
● Step 2: Mold Preparation
Select the Sand: Use a mixture of silica sand, clay, and water. Sometimes, additional materials like coal dust or cereal binders are added to improve the sand's properties.
Place the Pattern in the Flask: Place the pattern into a molding box called a flask, which is usually divided into two halves: the cope (upper half) and the drag (lower half).
Ram the Sand: Pack the sand tightly around the pattern using a ramming tool to create a firm and stable mold. The sand must be compacted enough to hold its shape but still allow gases to escape during the casting process.
● Step 3: Core Insertion (if needed)
Create Cores: If the part has internal features like holes or passages, cores are created separately. Cores are typically made of sand and can be supported by core prints in the mold.
Insert the Cores: Carefully place the cores into the mold to occupy the spaces that will become the internal cavities once the metal solidifies.
● Step 4: Remove the Pattern
Lift the Cope: Lift the upper half of the flask (cope) away from the lower half (drag), exposing the pattern.
Remove the Pattern: Carefully remove the pattern from the sand, leaving a cavity in the shape of the desired part.
● Step 5: Assemble the Mold
Place the Cope Back: Place the cope back on top of the drag, aligning the two halves of the mold.
Seal the Mold: Clamp the mold halves together to ensure they stay in place during the pouring process.
● Step 6: Pouring
Prepare the Metal: Melt the metal in a furnace to a specific temperature, depending on the type of metal being used.
Pour the Molten Metal: Pour the molten metal into the mold through a system of channels called gates and risers. The gates direct the flow of metal into the cavity, while the risers provide extra material to compensate for shrinkage during cooling.
● Step 7: Cooling and Solidification
Allow the Metal to Cool: The molten metal cools and solidifies inside the mold. The cooling time varies depending on the size and complexity of the part.
Control the Cooling Rate: In some cases, cooling rates are controlled to ensure uniform solidification and minimize defects.
● Step 8: Shakeout and Cleaning
Break the Mold: Once the metal has fully cooled and solidified, break apart the sand mold to remove the casting.
Remove Gates and Risers: Cut off the gates and risers from the casting, and remove any excess material.
Clean the Casting: Clean the casting to remove any remaining sand, scale, or other residues. This may involve sandblasting, grinding, or other cleaning methods.
● Step 9: Inspection and Finishing
Inspect the Casting: Inspect the casting for defects such as porosity, inclusions, or surface imperfections.
Perform Finishing Operations: If necessary, perform additional finishing operations such as machining, grinding, or painting to meet the required specifications.
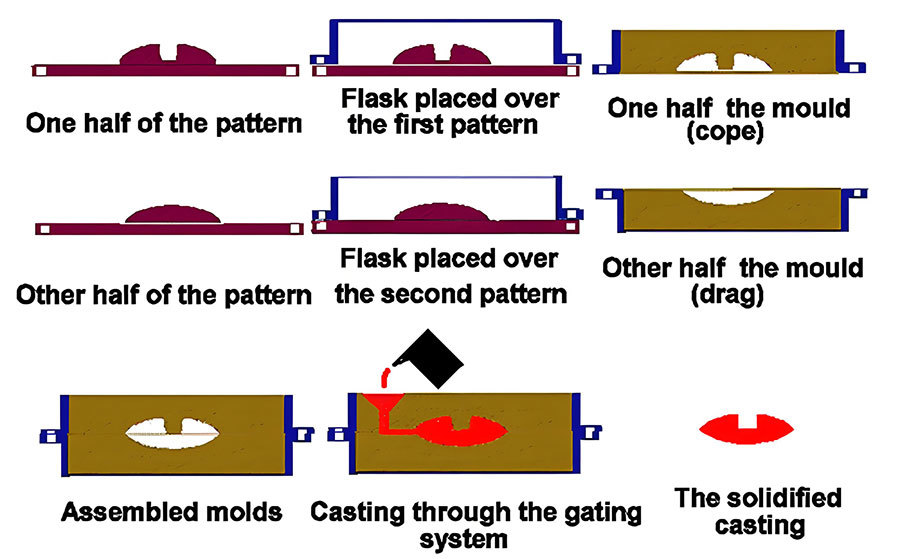
Sand casting Applications
Sand casting is a versatile and widely used metal casting process that can produce a wide range of parts and components. Its flexibility, cost-effectiveness, and ability to handle both simple and complex geometries make it suitable for various industries.
1. Automotive Industry
● Engine Components: Engine blocks, cylinder heads, pistons, crankshafts
● Transmission Parts: Gearboxes, transmission housings, gears
● Brake Systems: Brake calipers, brake drums, brake rotors
● Suspension Parts: Control arms, suspension links, shock absorbers
● Exhaust Systems: Manifolds, mufflers
2. Aerospace Industry
● Structural Components: Airframe components, engine mounts, landing gear parts
● Engine Parts: Turbine blades, compressor wheels, engine casings
● Interior Components: Seat frames, door panels, structural supports
3. Industrial Machinery
● Pumps and Valves: Pump bodies, valve bodies, valve seats
● Bearings and Bushings: Roller bearings, plain bearings
● Gears and Gearboxes: Spur gears, helical gears, bevel gears
● Housings and Frames: Machine housings, frames
4. Construction and Mining
● Heavy Equipment Parts: Excavator buckets, bulldozer blades, loader arms
● Structural Components: Beams, columns, support structures
● Mining Equipment: Drill bits, cutting tools, wear-resistant parts
5. Consumer Goods
● Household Appliances: Washing machine parts, dryer parts, refrigerator parts
● Cookware and Utensils: Pots, pans, kitchen tools
● Decorative Items: Statues, ornaments, architectural elements
6. Marine Industry
● Propellers and Shafts: Propeller blades, drive shafts
● Engine Parts: Marine engine blocks, cylinder heads, exhaust systems
● Structural Components: Hull components, deck fittings, anchor systems
7. Electrical and Electronic Industry
● Enclosures and Housings: Enclosures for electrical devices, housings for electronic devices
● Connectors and Terminals: Electrical connectors, terminal blocks
● Heat Sinks: Heat sinks for cooling
8. Medical Industry
● Surgical Instruments: Scalpels, forceps, clamps
● Prosthetics and Implants: Hip and knee replacements, dental implants
● Diagnostic Equipment: Parts for X-ray machines, MRI machines
9. Energy Sector
● Power Generation: Turbine blades, generator housings, cooling systems
● Oil and Gas: Drilling equipment, pipeline components, valves
● Renewable Energy: Wind turbine components, solar panel components, hydroelectric generators
10. Agricultural Equipment
● Tractors and Farm Implements: Tractor parts, plows, harrows
● Irrigation Systems: Irrigation system components, water management components
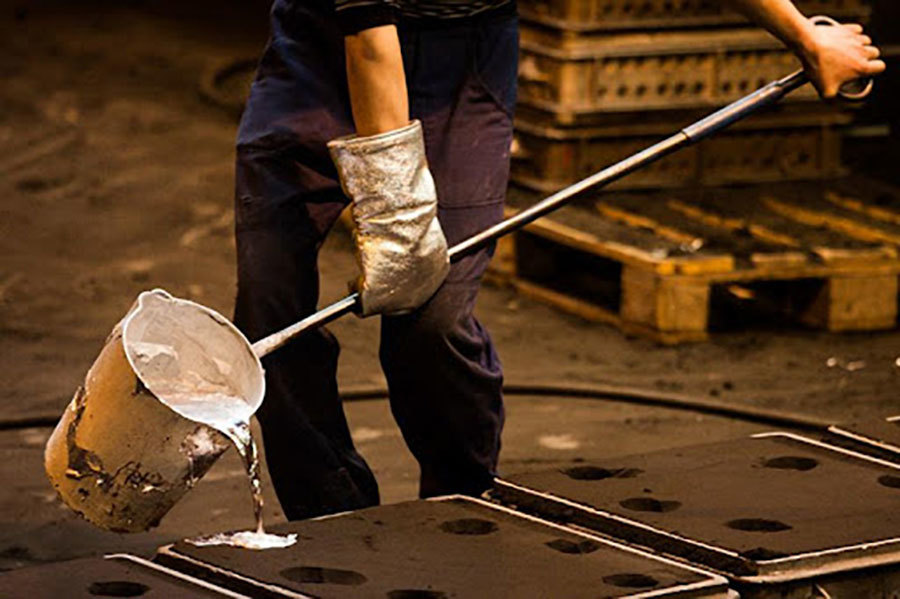
The Advantages & Disadvantages of Sand Casting
- Advantages of Sand Casting
1. Versatility: Sand casting produces parts with complex shapes and large sizes, making it suitable for a wide range of products.
2. Material Flexibility: This method can cast almost any metal, including ferrous and non-ferrous alloys, offering great versatility in material selection.
3. Low Tooling Costs: Initial tooling costs for sand casting are relatively low compared to other casting methods like die casting or investment casting.
4. Scalability: Sand casting is scalable and works well for both small batch production and mass production.
5. Recyclable: The sand used in the process can often be recycled and reused, reducing waste and cost.
6. Design Flexibility: Sand casting allows for a high degree of design flexibility, enabling the creation of intricate internal and external features.
- Disadvantages of Sand Casting
1. Surface Finish: Sand castings typically have a poorer surface finish than those produced by other casting processes, often requiring additional machining or finishing.
2. Dimensional Accuracy: While sand casting achieves reasonable dimensional accuracy, it is not as precise as some other casting techniques, especially for tight tolerance requirements.
3. Porosity and Inclusions: Sand casting is more prone to porosity and inclusions due to the nature of the sand mold, which can affect the strength and quality of the final product.
4. Labor Intensive: The process can be labor-intensive, particularly in preparing and removing the sand molds, increasing production time and costs.
5. Cooling Rate Variations: Cooling rates in sand casting can vary, leading to potential issues with material properties and structural integrity.
We would be happy to connect with you.
We will contact you within one working day. Please pay attention to your email.